Hose pipes are necessary for moving fluids in a variety of sectors, from equipment to gardening watering. They ensure efficient fluid transfer for numerous tasks. Understanding the types, components, installation, and maintenance of hose pipes is vital for optimal performance. This guide offers practical insights and expert advice to help you make informed decisions and maximise the effectiveness of hose pipes. Join us as we explore the intricacies and possibilities of hose pipes in fluid conveyance and beyond.
Types of Hose Pipes
- Garden Hose Pipes: Garden hose pipes are versatile tools commonly used in households and outdoor spaces. Made of rubber or PVC, these hoses come in various lengths and diameters, catering to different needs such as watering plants or cleaning vehicles.
- Watering Hose Pipes: Specifically designed for irrigation purposes, watering hose pipes feature specialised nozzles or sprinklers to distribute water evenly over plants and gardens, crucial for maintaining healthy vegetation.
- Industrial Hose Pipes: Heavy-duty conduits used in industrial settings for transporting fluids under high pressure and harsh conditions, industrial hose pipes are designed to withstand abrasion, corrosion, and extreme temperatures, finding applications in diverse industries.
- Hydraulic Hose Pipes: Transmitting hydraulic power in hydraulic machinery, these hoses are vital in construction equipment, agricultural machinery, and industrial machinery, requiring high-pressure resistance and excellent flexibility.
- Fire Hose Pipes: Essential firefighting equipment used to extinguish fires by delivering water or other firefighting agents, fire hose pipes are designed to withstand high pressure and heat, ensuring effective firefighting operations.
- Suction Hose Pipes: Used for suction applications such as pumping water or fluids, suction hose pipes are commonly employed in construction, agriculture, mining, and wastewater management, reinforced to prevent collapse under vacuum pressure.
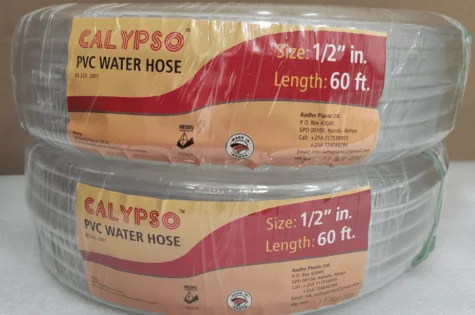
Components of a Hose Pipe
- Inner Tube: The inner tube is the core component where fluid flows. It’s made from materials like synthetic rubber or PVC, chosen for compatibility with the specific fluid being transported.
- Reinforcement Layer: This layer provides structural support, preventing the hose from collapsing or bursting under pressure. It’s typically constructed from high-strength materials such as synthetic fibers, wire braids, or metal spirals.
- Outer Cover: The outer cover protects the hose from external damage, including abrasion, weathering, and other environmental factors. It’s usually made from durable materials like synthetic rubber, PVC, or thermoplastic compounds.
- Fittings and Connectors: These components are crucial for assembling and connecting hose pipes. They ensure leak-free connections and maintain optimal performance of the hose system.
Uses of Hose Pipes
- Watering and Irrigation: Hose pipes are essential for watering plants, lawns, and gardens, providing an efficient way to distribute water. Equipped with sprinklers or drip systems, they conserve water and deliver precise amounts to targeted areas.
- Cleaning and Washing: Hose pipes are crucial for cleaning outdoor spaces, vehicles, equipment, and surfaces. High-pressure hoses are particularly effective for heavy-duty tasks like removing mud, grease, and stains.
- Construction and Manufacturing: In construction and manufacturing, hose pipes convey water, air, chemicals, and hydraulic fluids, supporting machinery such as pumps, compressors, and pneumatic tools. They are vital on construction sites, in factories, and on assembly lines.
- Agriculture and Farming: Hose pipes are used for irrigation, spraying pesticides and fertilisers, and transferring water. They help farmers manage water resources, enhance crop yields, and maintain soil fertility.
- Firefighting and Emergency Response: Fire hose pipes enable firefighters to deliver water or agents to extinguish fires, protecting lives and property. These hoses must meet strict standards for pressure resistance and durability.
- Automotive and Transportation: In these industries, hose pipes are used for cooling systems, fuel delivery, brakes, and air conditioning, ensuring efficient transfer of fluids and gases for optimal vehicle performance and safety.
Selection Criteria for Hose Pipes
- Application Requirements: Identify the specific needs, including fluid type, pressure, temperature, environmental conditions, and regulatory standards. Select hose pipes with suitable materials, construction, size, and features for optimal performance and safety.
- Material Compatibility: Ensure the hose material is compatible with the fluid to avoid chemical reactions, contamination, or degradation. This includes resistance to acidity, alkalinity, corrosiveness, and toxicity, ensuring system integrity and longevity.
- Pressure Rating: Choose a hose pipe with a pressure rating exceeding the system’s maximum operating pressure to prevent bursting or leakage. Consider static, dynamic, pulsation, and surge pressures, opting for a higher rating for added safety.
- Temperature Range: Select a hose that operates within the fluid and environmental temperature ranges. Ensure it withstands extreme temperatures without losing flexibility or durability, preventing premature failure.
- Flexibility and Bend Radius: Ensure the hose has adequate flexibility and bend radius for easy installation and handling, preventing kinking or collapsing. This supports smooth operation and prevents flow path obstructions.
- Length and Size: Choose the correct length and size based on the distance, flow rate, and pressure requirements. Proper selection prevents pressure drops, friction losses, and flow restrictions, considering hose expansion, contraction, and coiling.
- End Connections: Use compatible end connections, such as couplings or adapters, for secure, leak-free connections. Ensure they match the hose material, size, and thread type, providing reliable system integration and minimising leaks or accidents.
Materials Used in Hose Pipes
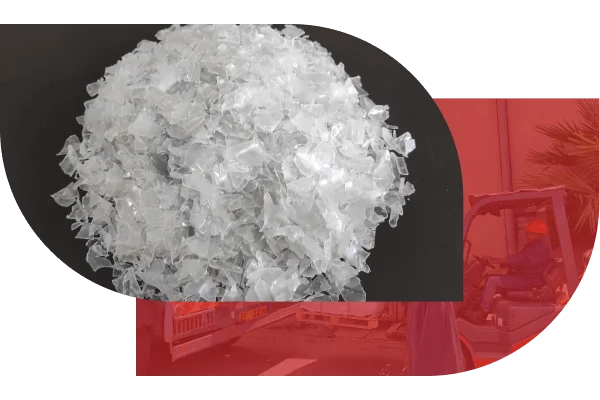
Material selection is crucial in hose pipe manufacturing, impacting performance and durability. Various materials like synthetic rubber, PVC, metal wire, and thermoplastics are used for strength, flexibility, and environmental resistance. Additionally, businesses often consider factors such as hot washed pet flakes price when selecting materials for hoses used in specific applications, particularly in industries where cost-effectiveness and material quality are paramount.
Here, we explore common materials in hose pipes with descriptions and applications. Understanding them aids in choosing suitable hoses for specific needs.
Material | Description |
Synthetic Rubber | Durable and flexible material commonly used for hose pipe inner tubes. Offers excellent resistance to abrasion, tearing, and weathering for various applications. |
PVC (Polyvinyl Chloride) | Versatile plastic material used for both inner tubes and outer covers. Lightweight, corrosion-resistant, and cost-effective, ideal for flexible and affordable applications. |
Synthetic Fibers | Polyester or nylon fibers provide structural support in the reinforcement layer. High tensile strength and resistance to stretching ensure hoses withstand high pressures. |
Metal Wire | Steel or aluminum wire reinforcement adds strength and durability to heavy-duty hoses. Enhances resistance to internal and external forces, ideal for industrial use. |
Thermoplastic Materials | Polyurethane or polyethylene outer covers protect against abrasion, UV radiation, and chemicals. Offers flexibility, impact resistance, and wearability for outdoor use. |
Brass | Brass fittings and connectors offer excellent corrosion resistance, machinability, and durability. Ensure secure, leak-free connections in hose pipe systems. |
Stainless Steel | Preferred for superior corrosion resistance and hygiene in food processing, pharmaceuticals, and chemicals. Provides strength, durability, and compatibility with fluids. |
Installation and Maintenance of Hose Pipes
- Inspection and Testing: Before installation, thoroughly examine hose pipes for damage or defects. Conduct a pressure test to ensure integrity and performance, replacing any faulty pipes.
- Handling and Storage: Handle with care to prevent damage. Store in a clean, dry area away from heat and chemicals, coiling or hanging to maintain shape.
- Installation Procedures: Follow manufacturer guidelines. Route and support pipes properly to prevent stress or movement, avoiding sharp bends.
- Maintenance: Establish routine inspections and cleaning. Replace worn components to preserve functionality and hygiene.
- Safety Precautions: Wear appropriate gear and exercise caution with high-pressure pipes to prevent injury.
- Troubleshooting and Repairs: Address malfunctions promptly, identifying and resolving issues to ensure continued operation and compliance.
Conclusion
Hose pipes are essential for fluid conveyance, offering versatility and efficiency. Understanding their types, components, uses, and maintenance is crucial for maximizing their potential. Follow this guide for informed decisions, ensuring optimal performance and safety in applications. Embrace the power of hose pipes to elevate fluid conveyance capabilities. Trust Radhe Plastic Ltd for premium-quality hoses and expert solutions, that surpass expectations.