Hydraulic cylinders are essential components in various industries, such as construction, agriculture, manufacturing, and aerospace. They provide the force needed to move or lift heavy loads, making their operational performance crucial for efficiency, safety, and productivity. To meet the demands of modern applications, hydraulic cylinder manufacturers are constantly innovating to improve their products. This article explores how these manufacturers enhance operational performance through design enhancements, material selection, technological advancements, and more.
NOTE – Hydraulic Cylinder Manufacturer: Power Hydraulics has been known for providing innovative and reliable hydraulic cylinders. Their commitment to quality and customer satisfaction has made them a trusted name in the industry.
Design Enhancements
The design of hydraulic cylinders plays a significant role in their performance. Manufacturers focus on several key aspects to improve the efficiency and reliability of their cylinders:
Optimized Sealing Systems
A high-quality sealing system is vital for the proper functioning of hydraulic cylinders. Manufacturers are continually refining seals to handle extreme pressures, temperatures, and various operating conditions. Improved sealing systems reduce the risk of leaks, maintain operational efficiency, and extend the lifespan of the cylinders.
Stronger, Lighter Materials
Using advanced materials such as high-strength steel, stainless steel, and composites allows manufacturers to make cylinders that are both lighter and more durable. Lighter cylinders are easier to handle and install, while stronger materials ensure better performance under pressure, resulting in longer operational life.
Improved Piston Designs
The piston is a core component in hydraulic cylinders. By refining piston designs to reduce friction and wear, manufacturers can enhance performance and reduce energy consumption. Optimized pistons can carry heavier loads and operate more efficiently, improving the overall functionality of the cylinder.
Material Selection and Quality Control
Choosing the right materials is essential for creating hydraulic cylinders that are reliable and long-lasting. The selection of materials and rigorous quality control are essential to improving performance.
High-Strength Alloys
Many manufacturers now use high-strength alloys for better performance in challenging applications. These materials provide superior resistance to wear, corrosion, and fatigue, ensuring that cylinders can withstand the toughest conditions.
Surface Coatings and Treatments
Cylinders operate under high pressure and friction, which can lead to wear. To combat this, manufacturers use coatings and surface treatments to improve wear resistance, reduce friction, and protect against corrosion. These treatments extend the cylinder’s life and ensure it performs at its best.
Strict Quality Control Processes
Manufacturers implement stringent quality control measures, such as non-destructive testing (NDT), to ensure that each cylinder meets high standards. These processes detect any flaws early, reducing the risk of failures during operation and ensuring reliable performance.
Technological Advancements
With the rise of modern technology, hydraulic cylinder manufacturers are embracing new tools and techniques to improve performance:
Computer-Aided Design (CAD)
By using CAD software, manufacturers can design and simulate hydraulic cylinders before they are physically created. This allows engineers to optimize designs for efficiency and reduce the likelihood of errors. CAD also helps in creating custom cylinders tailored to specific applications.
Integration of Smart Sensors
Incorporating smart sensors into hydraulic cylinders is one of the latest advancements in the industry. These sensors collect real-time data on pressure, temperature, and displacement, enabling better monitoring and predictive maintenance. By detecting potential issues early, these sensors help reduce downtime and improve the overall performance of hydraulic systems.
Advanced Manufacturing Techniques
Additive manufacturing (3D printing) and precision machining are transforming the way hydraulic cylinders are made. These techniques allow for greater design flexibility, faster production times, and the ability to produce more complex components. They also reduce waste and improve the precision of the final product.
Customization for Specific Applications
Not all hydraulic cylinders are created equal. Depending on the industry or application, manufacturers may need to create custom solutions to improve performance. Tailored cylinders meet specific needs, such as working in harsh environments or dealing with unique loads.
Tailored Stroke Lengths and Diameters
The stroke length and diameter of a hydraulic cylinder significantly impact its performance. Manufacturers offer customization options to design cylinders with the perfect specifications for a given application. This ensures the cylinder operates at its best and maximizes efficiency.
Pressure and Temperature Tolerances
In industries such as mining or offshore drilling, hydraulic cylinders must endure extreme pressure and temperature conditions. Manufacturers can customize cylinders with higher pressure and temperature ratings to ensure they can perform reliably under these tough conditions.
Specialized Sealing Materials
Hydraulic cylinders that operate in extreme conditions, such as underwater or in dusty environments, require special sealing materials. Manufacturers use advanced seals that are resistant to corrosion, contaminants, and temperature extremes, ensuring the cylinder performs efficiently even in harsh conditions.
Preventing Common Issues and Enhancing Maintenance
One of the best ways to improve the operational performance of hydraulic cylinders is to prevent common issues such as leakage, contamination, and excessive wear. Manufacturers focus on solutions that minimize these problems and enhance overall maintenance:
Leak Prevention
Leaks can lead to inefficiencies and higher maintenance costs. Manufacturers improve sealing systems to prevent leaks and ensure better cylinder performance. This contributes to longer life and reduced maintenance needs.
Contamination Control
Contamination from dirt, dust, or moisture can damage hydraulic systems. By using better filtration systems and enhanced sealing designs, manufacturers can minimize the risk of contaminants entering the cylinder, protecting its performance.
Maintenance-Friendly Designs
Many modern hydraulic cylinders are designed with maintenance in mind. Features such as replaceable seals or accessible inspection points make routine maintenance quicker and more cost-effective, reducing downtime and keeping systems running smoothly.
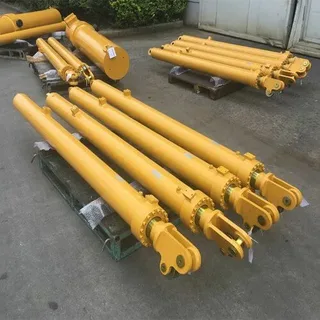
Conclusion
Hydraulic cylinder manufacturers are constantly striving to improve the operational performance of their products. Through innovative design changes, material enhancements, advanced technologies, and custom solutions, they ensure that their cylinders meet the high demands of modern industries. Whether through optimizing sealing systems, using stronger materials, or incorporating smart sensors, manufacturers are enhancing the reliability and efficiency of hydraulic cylinders. These improvements not only make hydraulic systems more effective but also reduce maintenance costs and increase the overall lifespan of the cylinders.
For More Insightful Articles Related to This Topic, Feel Free to Visit: trendingblogsweb