From chemical processing to HVAC systems, air cooled heat exchangers are a vital part of many industrial uses including power generation. In areas with water shortage or where water treatment expenses are prohibitive, their capacity to effectively transfer heat without water use makes them priceless. To guarantee best performance and lifetime, these systems do, however, like other industrial equipment depend on regular maintenance. Not only does proactive maintenance avoid unplanned downtime but it also greatly increases the operational life of your investment. This all-inclusive book looks at key maintenance techniques that can improve the lifetime of your air cooled heat exchangers and guarantee constant performance and energy economy.
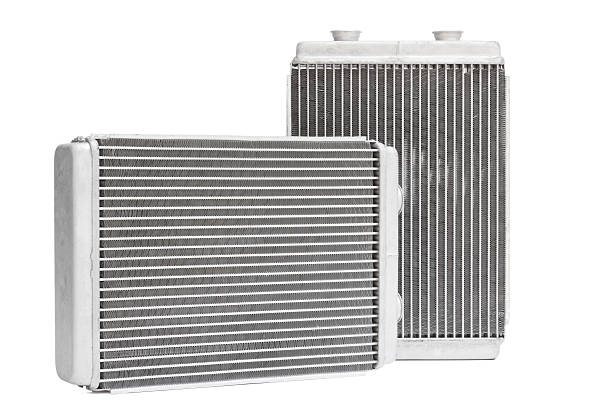
Knowing Components of an Air Cooled Heat Exchanger
One should first grasp the basic parts of air cooled heat exchangers before diving into maintenance practices. Usually comprising finned tubes where the process fluid flows, these systems include fans to move ambient air across the tubes, motors to control the fans, and supporting structures. As air flows across the finned tubes, the heat transfer cools the process fluid within. Features including fin design, tube material, air flow pattern, and environmental conditions affect the effectiveness of this heat transfer mechanism.
Because of its outstanding corrosion resistance and longevity, stainless steel heat exchangers find use in many different kinds of industry. In demanding settings when exposure to corrosive fluids or atmospheric conditions would degrade other materials, stainless steel heat exchangers provide exceptional performance. Applying efficient maintenance plans that target certain system vulnerabilities depends on an awareness of these elements and their interplay.
Frequent Cleaning and Debris Removal
The collection of dirt, trash, and pollutants on the outside surfaces of the finned tubes is one of the most often occurring problems influencing the operation of air cooled heat exchangers. This build-up forms an insulating barrier that greatly lowers heat transfer efficiency and raises system energy consumption. Maintaining best performance so depends on a consistent cleaning regimen.
Quarterly cleaning might be plenty for regular industrial settings; nonetheless, facilities in dusty areas or those handling materials that generate airborne particulates may call more frequent attention. Larger trash should first be removed with compressed air, then a more complete cleaning using suitable cleaning products should follow. Using cleaning agents free of compromise of the passive oxide layer offering corrosion resistance is crucial for stainless steel heat exchangers. Steer clear of abrasive tools that can cut the surface of the fins or tubes since these scratches could start corrosion or fouling.
Fin and Tube Inspection and Repair
Physical impact, erosion, and corrosion are only a few of the several types of damage experienced by the fins and tubes of air cooled heat exchangers. Frequent checks help to find bent or damaged fins, which could block airflow and lower the heat transfer efficiency. Bent fins can be straightened with specialized fin combs; nevertheless, this must be done carefully to prevent more damage.
Similarly crucial are tube inspections, especially for stainless steel heat exchangers that could be vulnerable to various kinds of corrosion depending on the surroundings and process fluids. To find wall thinning, pitting, or cracking, inspection techniques could call for ultrasonic testing, ocular inspection, or eddy current analysis. Any found flaws should be taken care of right away since localized harm can spread fast and cause more general concerns. Sometimes individual tubes might have to be replaced or closed in order to keep system integrity and stop cross-contamination between process fluids and the cooling air.
Fan and Motor Maintenance
Another important maintenance concern is the fans and motors running air circulation through air cooled heat exchangers. These parts need constant care to make sure they continue to offer the intended airflow since they are mechanical wear targets. Fan blades should be checked for balance since unbalanced operation could cause vibration that compromises the heat exchanger structure as well as the fan assembly.
Usually including manufacturer requirements for lubrication of bearings, alignment check, and monitoring of electrical characteristics including current draw and insulating resistance, motor maintenance also includes To find early indicators of bearing wear or imbalance before they cause catastrophic failure, many buildings are now running vibration analysis programs. Furthermore, whether belts, gears, or direct drives, the drive systems that link motors to fans call for particular maintenance to guarantee effective power transfer. Maintaining design heat transfer rates depends on constant airflow over the heat exchanger, so well maintained fan systems guarantee this.
Techniques of Corrosion Protection
Particularly in demanding conditions, corrosion is one of the most major risks to the lifetime of heat exchangers. Though they have natural corrosion resistance, stainless steel heat exchangers are not impervious to all types of corrosion. Different approaches can be used to improve protection starting with appropriate material choice throughout the design process. Higher-grade stainless steels or specialty alloys can be required for especially demanding uses.
Although they offer a further barrier against corrosive elements, protective coatings must be carefully chosen to guarantee they do not restrict heat flow. Identification of possible corrosion hazards before they cause major damage depends on consistent monitoring of water chemistry (for hybrid systems) and process fluid parameters. Sometimes cathodic protection may be achieved via impressed current systems or sacrificial anodes. Maintaining the passive oxide layer is essential for stainless steel heat exchangers, so in some uses regular passivation treatments are quite important.
Performance Tracking and Improvement
Starting a thorough performance monitoring program offers insightful analysis of the efficiency and condition of air cooled heat exchangers. Important characteristics to track include fan power consumption, process fluid pressure drop throughout the exchanger, and approach temperature—that is, the difference between the exit process fluid temperature and the input air temperature. Variations from normal values might point to growing issues needing action.
Digital monitoring systems that offer real-time heat exchanger performance are the backbone of modern facilities. These systems enable quick investigation and corrective action by setting alarms when criteria stray from reasonable ranges. Periodic thermal imaging can also point up hotspots in certain places that might suggest blocked tubes or poor airflow. Monitoring for particular kinds of corrosion that could compromise this material is especially crucial for stainless steel heat exchangers since early discovery helps to avert more severe damage.
Winterizing and Seasonal Considerations
Operating in areas with considerable seasonal temperature fluctuations, air cooled heat exchangers present particular difficulties that call for particular maintenance issues. Frozen tubes can cause catastrophic failures and prolonged downtime in colder climes. Among the several winterizing techniques available are louver systems to control airflow, hot air recirculation, or heating system installation to stop freezing.
On the other hand, operations in very hot surroundings could need adjusted maintenance plans or extra cooling capacity to consider the higher thermal stress on components. Before the start of severe storms, seasonal maintenance plans should incorporate extensive actions in preparation and inspection. The maintenance plan for stainless steel heat exchanger has to take thermal expansion and contraction related with temperature cycling into account since this can strain tube-to– header joints and other important connections.
Conclusion
A major investment in operational dependability and equipment lifetime is making a thorough maintenance program for air cooled heat exchangers top priority. Facilities may greatly extend the lifetime of these essential systems by concentrating on consistent cleaning, component inspection, corrosion protection, and performance monitoring, therefore reducing energy usage and unanticipated downtime. The particular needs will differ depending on the application, surroundings, and heat exchanger design; so, it is imperative to create a customized maintenance plan that meets the particular difficulties your facility presents. Particularly in corrosive locations or applications needing strict hygienic standards, stainless steel heat exchangers can offer a great mix of performance, durability, and lifetime cost when evaluating improvements or replacements for aged systems. See experts at Kinetic Engineering Corporation for professional advice on preserving or modernizing your heat exchange systems; their customized solutions based on decades of industry knowledge will be highly appreciated.